
MAGNA

HYGIENIC DIRECT DRIVE MOTORS

The power of
MAGNA
TORQUE
Equivalent to 1HP 30:1 with a fairly flat torque curve from 1-250 Rpm
Leading to Reduced Costs, Longer Lifespan, No Maintenance and with Improved Product Quality.
What are MagnaTorque Direct Drive Motors?
Direct Drive Permanent Magnet Synchronous Motors (PMSM), share the common characteristic of directly driving the load without the need for a transmission or gearbox.
In industries where Floor space is limited and expensive and where hygiene is important and/or maintenance cost is high, direct drive torque motors offer the opportunity to save costs and to boost productivity.
In addition, it reduces motor size by a factor of 2 to 3 compared to conventional induction motor/gearboxes. Reducing floor space and cost of ownership.
These Permanent Magnet Synchronous Motors (PMSM) are increasingly being used in food processing applications due to their high efficiency, high power density, and compact size.
By using these motors, engineers within the Food Industry are able to design conveyors and machinery that is more energy-efficient, compact, and precise, with our without our encoder option.

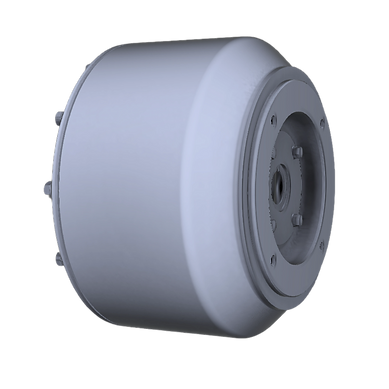
“Leading to Reduced Costs, Longer Lifespan, No Maintenance and with Improved Product Quality.”
specifically designed for
Food processing machinery
and
conveyance industries
What is an Outrunner Motor?
An outrunner motor is a type of Permanent Magnet Synchronous Motor (PMSM) with a unique design. It consists of a stator with coils and a rotor with permanent magnets. In contrast to inrunner motors, where the magnets are attached to a shaft inside the stator coils, in an outrunner motor, the magnets are attached to a ring or sleeve on the outside of the stator coils. This results in the motor having a rotating ring or sleeve instead of a rotating shaft.
Outrunner motors produce more torque for the same build volume compared to inrunner motors.
STATOR & ROTOR

Peak Torque
ranging from
339.8 Nm
Continuous Torque ranging from
0.5 - 110Nm
Up to 600V DC
bus voltage
Highly efficient
Outer Diameter ranging from 40-485 mm
Quiet operation and compact design
Temperature Sensor
(optional)
High Torque density
Very high lifetime
Magnets
Rotor ring
Low cogging
m1 and M2 series
Natural convection
Performance
Parameters | Unit | M1 225 | M1 250 | M1 275 |
---|---|---|---|---|
Peak Torque (*) | Nm | 113,3 | 226,5 | 339,8 |
Stall Torque (***) | Nm | 36,8 | 62,6 | 83,7 |
Torque constant at 20°C | Nm/Arms | 9,0 | 18,0 | 27,0 |
Motor constant at 20°C | (Nm)2/W | 21 | 50 | 85 |
Max. No load speed | rpm | 780 | 390 | 250 |
Thermal resistance | K/W | 0,57 | 0,49 | 0,46 |
Continuous torque (***) | Nm | 47,8 | 81,9 | 110,4 |
(*) 8 K/sec temp increase rate / (**) terminal to terminal / (***) @ 140 °C coil temp / Ambient temperature = 20°C, Max. allowed coil temperature = 160°C. Default temperature sensor PT1000.
electrical
Parameters | Unit | M1 225 | M1 250 | M1 275 |
---|---|---|---|---|
Continuous torque (***) | Arms | 6,0 | 5,1 | 4,5 |
Peak Torque (*) | Arms | 28 | 28 | 28 |
Stall Current (***) | Arms | 4,5 | 3,8 | 3,4 |
Back EMF constant (**) | Vrms/rpm | 0,544 | 1,087 | 1,6 |
Line - line resistance at 20°C | Ω | 2,611 | 4,305 | 5,7 |
"Line - line induction, LLL" | mH | 35 | 58 | 81 |
Max. Continuous Power Dissipation | W | 211 | 245 | 261 |
Motor type Max DC bus Voltage | VDC | 600 | 600 | 600 |
(*) 8 K/sec temp increase rate / (**) terminal to terminal / (***) @ 140 °C coil temp / Ambient temperature = 20°C, Max. allowed coil temperature = 160°C. Default temperature sensor PT1000.
mechanical
Parameters | Unit | M1 225 | M1 250 | M1 275 |
---|---|---|---|---|
Motor Length | mm | 49 | 74 | 99 |
Lamination Stack Length | mm | 25 | 50 | 75 |
Pole pairs | - | 16 | 16 | 16 |
Rotor Inertia | g,m2 | 21 | 40 | 58,9 |
Stator Mass (excl. watersleeve) | kg | 5,8 | 11,52 | 17,28 |
Rotor Mass | kg | 1,45 | 2,75 | 4,05 |
Total Mass | kg | 7,25 | 14,27 | 21,33 |
Stator inner diameter | mm | 115 | 115 | 115 |
Rotor outer diameter | mm | 250 | 250 | 250 |
(*) 8 K/sec temp increase rate / (**) terminal to terminal / (***) @ 140 °C coil temp / Ambient temperature = 20°C, Max. allowed coil temperature = 160°C. Default temperature sensor PT1000.
KEY FEATURES OF
MAGNATORQUE
-
Unique form factor & Compact size
-
SAE C face on both sides
-
Complete Hollow bore 1.25”
-
High position accuracy with or without encoders
-
Fast response to load and position variations
-
Horizontal, vertical and diagonal mounting capability
-
Zero motor maintenance
-
Zero Backlash,
-
No vibration
-
Compatible with industry standard
-
Motor drives (3-phase)
-
IP69K rated, SS 316L
-
High torque, low speed motors
-
Hollow Bore shaft (no more customized conveyor drum motors)
-
Compact size
-
High dynamics
-
High torque density
-
High efficiency
-
Optimal speed control
-
High reliability and lifetime
-
Low maintenance
-
Quiet operation
-
No more Oil leaks or Gearboxes to maintain
POWERING INNOVATION
Engineers working in the food industry face several challenges when developing an application, including food safety, sustainability, and equipment maintenance. One major advantage of our direct drive motors is that they are low in maintenance, thus reducing expensive downtime and maintenance costs.
In a production environment, time is often of the essence, and any downtime can have a significant impact on productivity and profitability. By integrating a motor from MagnaTorque, it is possible to reduce the number of unscheduled maintenance stops and keep the production line running smoothly.
Because of the high efficiency our MagnaTorque motors, you can convert a high percentage of their input electrical power into useful mechanical power, resulting in less heat generation and lower energy costs. Compared to brushed motors, the absence of AC brushless induction motor/gearbox applications, our direct drive motors eliminate mechanical wear and gear vibrations.
“The load is directly driven by the motor. No gearboxes, worm gear drives, oil or other transmissions necessary.”
This reduces the moving parts in the system, resulting in high operational life and reliability, while reducing the overall system cost.
These motors are able to deliver a high amount of power in a small package, making them ideal for applications where space is at a premium. In food processing applications, this can be particularly useful as it allows for smaller, more compact machinery that can be easily integrated into existing production lines.
Our new, PMSM direct drive motors offer a number of benefits for food processing applications.
APPLICATION
MagnaTorque outer-runner electromagnetic technology-based products are utilized to build unique applications to deliver compact form factors with high performance in the Food processing industry. Our direct drive (torque) motors can help to reach new levels of efficiency and productivity even under the most demanding conditions.
Possible applications for our motors in the food industry are:
-
Conveyor Belts
-
Mixers & Blenders
-
Slicers & Dicers
-
Grinders & Choppers
-
Packaging Machinery
-
Semi Conductor
-
Automation Systems